
How Chemical Plants Choose Oil-Free Water-Lubricated Air Compressors: Key Points and Selection Guide
In chemical production, air quality directly affects product quality, process stability, and equipment lifespan. Oil-free water-lubricated air compressors have become the preferred equipment in the chemical industry due to their oil-free pollution, low maintenance costs, and high energy efficiency. This article provides a scientific selection guide for chemical plants from technical parameters, industry standards, and selection points.
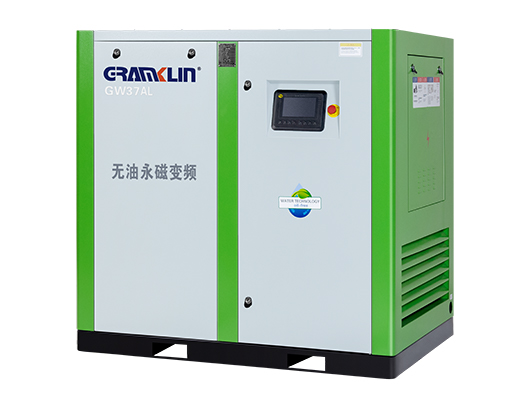
How Chemical Plants Choose Oil-Free Water-Lubricated Air Compressors: Key Points and Selection Guide
I. Core Advantages of Oil-Free Water-Lubricated Air Compressors
No Oil Pollution
Traditional oil-lubricated air compressors may mix oil mist into compressed air due to lubricant leakage, contaminating chemical raw materials or products. Oil-free water-lubricated air compressors achieve zero oil contact through special sealing technologies (such as piston rings and ceramic coatings), ensuring compressed air purity meets ISO 8573-1 Class 0 standards.
Adaptability to Harsh Environments
Chemical workshops often face complex conditions such as high temperatures, high humidity, and corrosive gases. Oil-free water-lubricated air compressors use corrosion-resistant materials (e.g., aluminum alloy, stainless steel) and enhanced cooling systems, enabling stable operation in environments ranging from -20°C to 50°C.
Energy Efficiency
Permanent magnet variable frequency technology, optimized air circuit design, and low-friction components increase the energy efficiency ratio (COP value) of oil-free water-lubricated air compressors by over 20% compared to traditional models, significantly reducing energy costs for enterprises.
II. Key Parameters and Technical Indicators for Selection
Air Volume and Pressure Matching
– Air volume demand: Calculate the maximum instantaneous air consumption (unit: m³/min) based on production processes, ensuring the compressor’s rated flow has a 10%-20% margin.
– Pressure level: The common pressure range in the chemical industry is 0.7-1.0MPa. Special processes (e.g., high-pressure reactors) require customized high-pressure models (up to 3.0MPa).
Compressed Air Quality Standards
– Cleanliness: Must meet ISO 8573-1 requirements for solid particles (≤0.01μm), moisture (≤3ppm), and oil content (≤0.01mg/m³).
– Dew point temperature: For drying processes, select models with a dew point temperature ≤-40°C (e.g., paired with refrigerated or adsorption dryers).
Energy Efficiency Certification
Prioritize products certified by national energy-saving standards (e.g., GB 19153) or EU IE3/IE4 energy efficiency levels to save substantial electricity costs over long-term operation.
III. Special Considerations for Chemical Plant Selection
Explosion-Proof and Safety Design
In explosive gas environments (e.g., petrochemical workshops), choose explosion-proof air compressors (Ex IIB T3/T4 certified), with motors and electrical control systems complying with explosion-proof standards.
Noise Control
Workshop noise must adhere to the “Industrial Enterprise Noise Health Standard” (≤85dB). Opt for low-noise models or equipment with soundproof enclosures.
Corrosion Resistance and Protection Grade
– Surface treatment: Apply epoxy resin or PTFE coatings to resist acids, alkalis, and other corrosive substances.
– Protection grade: IP54/IP55 dustproof and waterproof designs suitable for humid and dusty environments.
IV. Recommendations for Brand and Service Selection
Priority on International Brands
Brands such as Granklin offer advantages in reliability, durability, and technological innovation.
Localized Service Capability
Choose brands with local service outlets to ensure rapid response to maintenance needs and minimize downtime losses.
Customized Solutions
For complex conditions (e.g., multi-unit联控, waste heat recovery), collaborate with manufacturer technical teams to develop tailored solutions.
V. Installation and Maintenance Key Points
Installation Environment
– Place the compressor in a well-ventilated, dry, and dust-free indoor area, with at least 1.5 meters of space for maintenance.
– Position the air intake away from pollution sources (e.g., dust, exhaust outlets) and install pre-filters.
Regular Maintenance
– Filter replacement: Replace air filters every 2000-3000 hours, and oil filters (if applicable) simultaneously.
– Cooling system cleaning: Clean radiators every six months to prevent scaling or oil blockages.
– Electrical inspection: Annually test motor insulation, contactor status, and control system stability by professionals.
VI. Conclusion
When selecting oil-free water-lubricated air compressors, chemical plants should comprehensively consider process requirements, environmental conditions, energy efficiency standards, and after-sales services. Through scientific selection and standardized maintenance, ensure long-term stable operation of equipment, safeguarding production safety and product quality.